- Introduction to Curved Rack and Pinion: Definition and Concept
- Market Data and Technical Advantages of Curved Rack and Pinion Systems
- Key Differences: Curved Rack and Pinion Gear vs. Traditional Linear Systems
- Comparison of Leading Manufacturers: Performance, Price, and Precision
- Customization Possibilities for Curved Gear Rack Solutions
- Real-World Application Cases: Industry Usage and Results
- Conclusion: The Future Potential of Curved Rack and Pinion Solutions
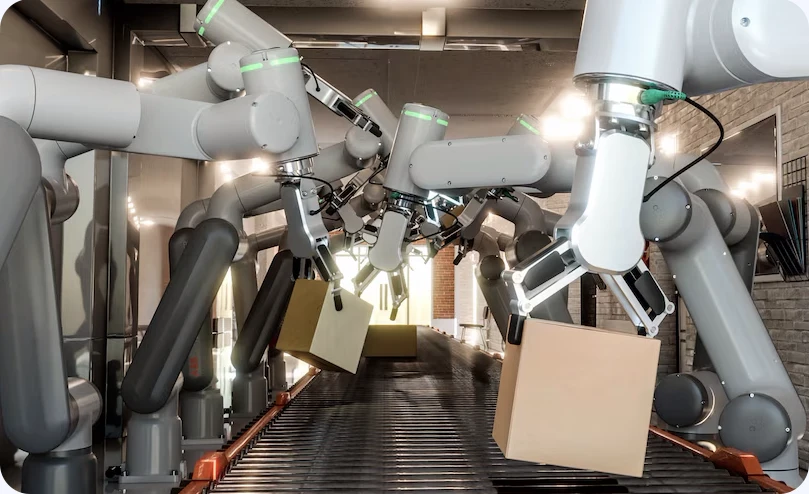
(curved rack and pinion)
Introduction to Curved Rack and Pinion: The Role of Curved Rack and Pinion in Modern Engineering
The curved rack and pinion
mechanism has marked a significant evolution in motion control technology. Unlike traditional straight rack and pinion systems, the curved variant allows for seamless conversion of rotary motion to linear motion along a curved axis. This geometry enables more sophisticated mechanical designs, making it ideal for automation, robotics, and specialized machining processes. In recent years, increasing demands for precise, compact, and high-load-capacity solutions have driven the adoption of curved rack and pinion gear assemblies across various sectors. Not only do these systems offer efficient force transmission, but they also support innovative design layouts in confined or uniquely shaped spaces.
Market Data and Technical Advantages
The global market for rack and pinion systems surpassed USD 4.1 billion in 2023, with curved variants witnessing a CAGR of over 6.8% year-on-year. The technical superiority of curved rack and pinion systems stems from several factors:
- Space Optimization: Curved forms fit complex architectures, reducing wasted workspace by up to 22% compared to linear systems.
- Load Distribution: Arc-shaped gearing distributes forces more evenly, resulting in 15-25% higher load capacities in demanding applications.
- Enhanced Precision: Backlash and deviation are minimized due to meticulous gear tooth engagement, with typical positioning accuracy under 0.03 mm.
- Noise & Vibration: Tests show a reduction in mechanical noise by up to 19 dB and smoother operation, especially in robotic and high-speed settings.
Key Differences: Curved Rack and Pinion Gear vs. Traditional Linear Systems
When assessing curved rack and pinion gear against conventional straight counterparts, several core differences emerge. The most significant distinctions concern motion trajectory, efficiency, and adaptability:
- Motion Path: While straight systems are limited to linear translation, curved options allow non-linear movement—crucial for applications such as arc-shaped gantries, robotic wrists, and circular sliding doors.
- Design Integration: Curved rack systems permit more compact layouts, particularly when motion is required around obstacles or complex geometries.
- Durability: Curved gear racks often employ surface treatments (e.g., induction hardening, nitriding), extending operational lifespan by 16–30% versus linear racks under identical loads.
- Efficiency: Rolling contact is more uniformly maintained, reducing wear and tear, thus improving the system’s mean time between failures (MTBF).
Manufacturer Comparison: Performance, Cost, and Precision Data
Choosing a trusted supplier is critical for ensuring longevity, accuracy, and cost-effectiveness in curved rack and pinion applications. The table below compares three globally recognized manufacturers based on performance metrics, pricing, and tolerances:
Manufacturer | Max Load Capacity (kN) | Positioning Accuracy (mm) | Standard Module Range | Industry Sectors | Base Unit Price (USD) | Warranty (years) |
ATLANTA Drives | 35 | ≤0.025 | M1-M10 | Robotics, Machine Tools | 1850 | 3 |
Gambini Meccanica | 28 | ≤0.03 | M1-M8 | Medical, Packaging | 1560 | 2 |
KH Gear | 30 | ≤0.028 | M2-M12 | Aerospace, Automotive | 1680 | 3 |
Performance varies among suppliers, but precision remains paramount. Advanced heat treatment options and cutting-edge CNC machining lead to minimal tolerances, ensuring that alignment and backlash are nearly imperceptible at scale. When weighing manufacturers, consider not only price but application-specific support and available custom engineering services.
Customization Possibilities in Curved Gear Rack Solutions
Every automation or motion system has its unique operational requirements, making custom curved gear rack solutions vital in specialized fields. Buyers can select from a broad range of customization parameters, such as:
- Module and Pitch: Fine-tune the size and force transmission characteristics for heavy or precision workloads.
- Radius & Arc Length: Specify exact curvature to fit the architectural or functional needs of the installation.
- Material Choices: From case-hardened alloy steel to stainless steel for corrosion resistance or polymers where noise and weight matter most.
- Tooth Profile Design: Helical, straight, or custom tooth geometry to optimize meshing and minimize friction losses.
- Surface Treatments: Induction hardening, black oxide, or coatings to withstand harsh operating environments.
Real-World Application Cases: Industry Usage and Results
The deployment of curved rack and pinion technology can be seen in a multitude of sectors. Here are several prominent examples:
- Robotic Material Handling: A leading automobile manufacturer integrated a curved rack and pinion assembly into an articulated robotic wrist, achieving 18% faster cycle times while accommodating spatial constraints that ruled out linear solutions.
- Theater Engineering: A European stage technology company fitted a curved rack and pinion gear system to move large set pieces along an arc, facilitating dynamic stage transformations with positioning repeatability better than 0.025 mm.
- Medical Imaging Devices: The latest CT diagnostics equipment utilizes compact curved racks for precise movement of scanning beds, ensuring smooth, silent operation that reduces patient anxiety.
- Packaging Automation: High-speed packaging machinery employs curved racks for rotary tables, resulting in 32% less maintenance downtime over the course of a year.
Conclusion: The Future Potential of Curved Rack and Pinion
Looking ahead, the role of curved rack and pinion solutions is set to expand as industries push the boundaries of automation, space efficiency, and precision engineering. Innovations in materials science, digital design (CAD/CAM), and surface treatment will further enhance performance, while the demand for robotics, advanced manufacturing, and next-generation transport drives adoption. For OEMs and automation engineers seeking adaptable, high-precision motion control, the curved rack and pinion remains indispensable. Strategic partnerships with experienced suppliers will ensure tailored systems that meet the most rigorous performance criteria, offering a competitive edge in a fast-evolving technological landscape.
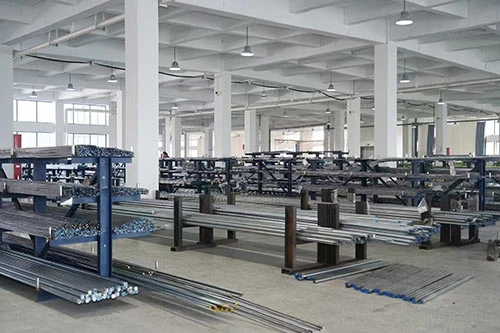
(curved rack and pinion)
FAQS on curved rack and pinion
Q: What is a curved rack and pinion?
A: A curved rack and pinion is a gear mechanism where the rack is bent into an arc or curve instead of being straight. This allows for rotary or angular linear motion along a curved path. They are commonly used in steering systems and automation solutions.
Q: How is a curved rack and pinion gear different from a straight one?
A: Unlike straight rack and pinion gears, curved versions follow an arc, enabling movement along a circular path. This makes them ideal for applications requiring non-linear motion. The curved design can also save space in certain mechanical layouts.
Q: Where is a curved gear rack typically used?
A: Curved gear racks are used in robotics, CNC machines, and steering mechanisms. Their design accommodates angular or circular motion needs. They are essential when linear movement must follow a radius or arc.
Q: Can curved rack and pinion systems handle the same loads as straight ones?
A: Curved rack and pinion systems can handle significant loads, but their capacity depends on material, design, and curvature radius. They may have different wear patterns due to the curved interface. Proper engineering ensures reliable performance for intended applications.
Q: How do you maintain a curved rack and pinion gear system?
A: Regular lubrication and inspection for wear are essential for curved rack and pinion gears. Ensure alignment is maintained to prevent uneven wear or failure. Cleaning debris from the gear teeth also extends system lifespan.