- Introduction: Overview of ball spline vs ball screw
and their significance in motion systems - Technical Overview: Key features and differences
- Performance and Efficiency: Evaluating load capacity, precision, and speed
- Manufacturer Comparison: Leading suppliers and product lines
- Customization and Integration: Adapting ball screw with ball spline designs to project needs
- Application Cases: Real-world examples in robotics, automation, and heavy machinery
- Conclusion: Summary of ball spline vs ball screw applications and recommendations
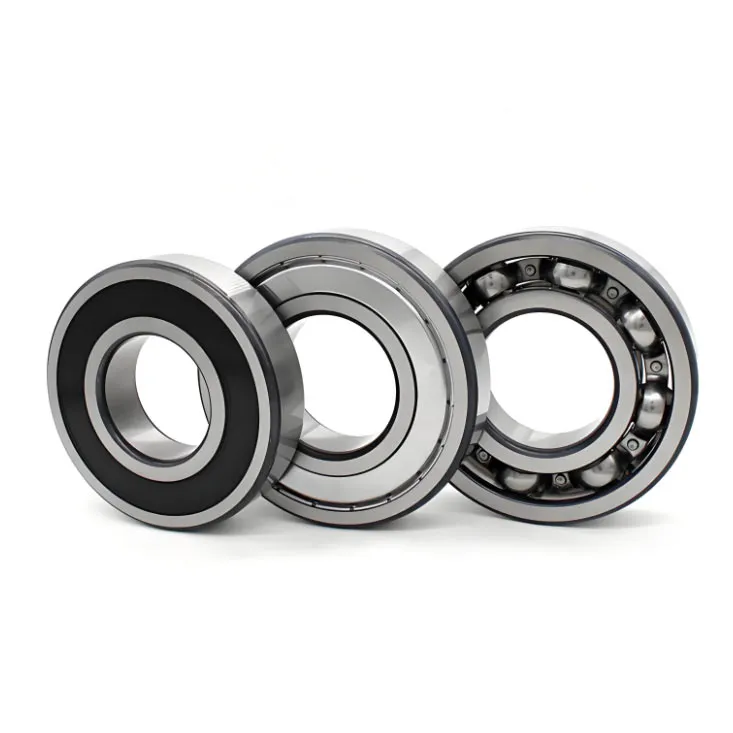
(ball spline vs ball screw)
Ball Spline vs Ball Screw: Introduction to Motion System Components
The advancement of industrial automation and robotics hinges significantly on high-precision linear and rotary motion systems. Among the solutions leading the pack are the ball spline and the ball screw, as well as innovative hybrid products like the ball screw with ball spline. Understanding the functional differences and applications of these components is crucial for system designers and engineering professionals aiming to improve efficiency, accuracy, and operational lifetime of their machinery. This article explores the key technical aspects, market options, and real-world usage of these technologies, culminating in guidance on selecting the optimal setup for varying requirements.
Technical Overview: Understanding Core Structure and Functionality
Both ball screws and ball splines excel at transmitting motion with minimal friction, but they operate on different mechanical principles. A ball screw translates rotary motion into linear travel using a spiral groove shaft combined with a matching nut filled with recirculating ball bearings. This design ensures positioning precision by drastically reducing backlash and operational wear. In contrast, a ball spline provides linear movement while simultaneously allowing for torque transmission, thanks to its grooved shaft and matching nut filled with ball elements. The result is a component capable of guiding loads along an axis with exceptional rigidity while accommodating rotational forces. The ball screw with ball spline or ball screw spline merges these traits, enabling simultaneous linear and rotary movement plus torque transfer in compact assemblies, which is vital for modern articulated mechanisms and compact robots.
Performance and Efficiency: Data-Driven Comparison
Vital criteria such as load capacity, travel speed, positioning accuracy, and operational life expectancy distinguish these solutions in practice. The table below compares performance metrics between premium ball screws, ball splines, and integrated ball screw spline units (figures are averaged from leading manufacturers):
Feature | Ball Screw | Ball Spline | Ball Screw Spline |
---|---|---|---|
Rated Axial Load (N) | 10,000 – 100,000 | 5,000 – 40,000 | 8,000 – 60,000 |
Torque Capacity (Nm) | 2 – 45 | 15 – 100 | 10 – 70 |
Maximum Linear Speed (mm/s) | 3,000 – 5,000 | 2,000 – 4,000 | 2,500 – 4,500 |
Backlash (mm) | <0.005 | <0.010 | <0.008 |
Positioning Accuracy (μm/m) | <10 | <15 | <12 |
Operational Life (cycles) | 2 million+ | 1.5 million+ | 1.7 million+ |
This data underscores that while ball screws offer leading precision and linear force delivery, ball splines excel in combining both guidance and high torque, and ball screw splines bridge the gap for complex, high-mix applications.
Manufacturer Comparison: Products and Innovations
In response to the growing demand for high-efficiency, compact, and durable motion solutions, several industry-leading manufacturers have developed specialized product lines in the ball spline, ball screw, and hybrid technology sectors.
THK and NSK dominate the global stage with robust ball screw offerings, while Nippon Bearing (NB Corporation) and HIWIN provide exceptional ball spline and ball screw spline configurations. A closer look at catalogue highlights reveals that THK’s LFK Ball Spline series emphasizes torque capacity, offering options above 90 Nm, while NSK’s Precision Ground Ball Screws prioritize ultrafine surface finish for accuracy below 8 μm/m. NB Corporation's SPB Series ingeniously integrates both ball screw and ball spline mechanics in a single, highly customizable component, catering to users seeking a more compact footprint. Cost, support, and accessory compatibility are additional differentiation elements, prompting buyers to consider total system fit, not just the standalone unit.
Customization and Integration: The Value of Tailored Solutions
Given the diverse operational environments, from semiconductor assembly lines to large-scale CNC machinery, off-the-shelf components seldom suffice in performance-critical motion systems. Recent industry surveys indicate that over 70% of automation integrators now specify customized elements in their orders, favouring products indexed to precise shaft diameters, thread pitches, ball recirculation configurations, and preloading schemes. The flexibility of ball screw with ball spline assemblies allows for:
- Integrated Nut Designs: Combining compact linear and rotary drive within single body formats.
- Material Enhancements: Specialty heat treatments and surface coatings enhance resistance to abrasive media and extend lifespan by up to 25%.
- Special Mounting Arrangements: Direct coupling to servo motors, custom brackets, or even cleanroom compatibility for critical industries such as medical device manufacturing.
Application Cases: Use in Modern Engineering
Real-world deployments shed light on the selection rationale behind these technologies. For instance:
- Articulated Robots: A leading European automotive manufacturer reduced arm payload variance by 18% by implementing hybrid ball screw spline components, enabling smoother simultaneous movements during welding operations.
- Medical Diagnostics: Laboratory automation systems replaced pneumatic slides with compact ball spline mechanisms, recording a 28% increase in throughput and lowering maintenance actions by a factor of four.
- Semiconductor Inspection: With sub-micron precision demanded, advanced ball screws with double nut preloads delivered less than 7 μm/m positioning error across 1.5 million cycles, allowing for more downtime between calibrations.
- Heavy Equipment: Retractable booms on mobile cranes now employ ball splines to transmit high torque while guiding the extension under heavy dynamic loads, substantially reducing system weight and hydraulic dependence.
Conclusion: Ball Spline vs Ball Screw Selection and Recommendations
In summary, the decision between ball spline vs ball screw, or to pursue integrated ball screw spline units, is dictated by the axis loads, torque, and multi-motion demands of each application. Ball screws remain unrivaled for pure linear accuracy at higher loads, while ball splines deliver optimal torque transfer with axis guidance, and hybrid ball screw spline assemblies answer the call for simultaneous multi-axis precision. For teams seeking to enhance reliability, decrease maintenance, and maximize footprint efficiency, consult closely with an application engineer and review the latest catalogues from top-tier manufacturers before finalizing a design. By leveraging the strengths of each motion component, engineers drive their systems to new levels of productivity and operational excellence.

(ball spline vs ball screw)