- Introduction to tensioner bearing
and its significance in mechanical systems - Technical advantages and performance characteristics of tensioner bearing, 6202 2rs bearing, and 6202 bearing
- Comparative manufacturer analysis with detailed data table
- Tailored solutions and customization offerings for tensioner applications
- Real-world application cases and performance insights
- Best practices for selection, installation, and maintenance of bearings
- Conclusion: The Future of tensioner bearing Technology and Its Industry Impact

(tensioner bearing)
Understanding Tensioner Bearing: The Foundation of Mechanical Drive Efficiency
In engineering applications where precise belt or chain tension is essential, the tensioner bearing forms a critical component of the power transmission system. Typically utilized to minimize slack and compensate for extending belts or chains, these bearings serve as the interface between rotating tensioner pulleys and their mounting structures. Through reducing vibrational impacts and wear, tensioner bearing designs contribute to longer machine lifespans and greater operational reliability.
The 6202 2rs bearing and 6202 bearing variants are particularly prevalent due to their standardized dimensions and robust sealing capabilities. Industrial reports show that equipment failures due to faulty tensioning account for up to 28% of unplanned downtime in conveyor and automotive systems. With machine maintenance costs surging globally, the emphasis on high-quality tensioner bearing integration becomes increasingly apparent.
Key Technical Advantages and Performance Insights
Precision-manufactured tensioner bearings deliver several quantifiable benefits that directly translate to improved performance and lower operational costs. Notably, the 6202 2rs bearing is engineered with double rubber seals, which offer enhanced protection against dust and contaminants, outlasting many open-type alternatives. Laboratory evaluations demonstrate that sealed deep groove ball bearings can retain lubrication 40% longer than shielded or open versions—even in exposure to moisture and particulate environments.
The 6202 bearing, known for its compact 15x35x11mm structure, supports dynamic radial loads exceeding 9,500N, while stationary axial loads remain effectively managed through its geometry. Additionally, specialized materials such as Chrome Steel (GCR15) provide significant corrosion and fatigue resistance, allowing operational temperature ranges from -40°C to +150°C.
Recognizing noise level, torque consistency, and rotational accuracy as critical parameters, data suggests that top-tier tensioner bearings achieve noise levels below 20 decibels during operation—deemed virtually silent in automotive engine bays and automated factory systems.
Comparative Data Table: Manufacturer Analysis
Evaluating suppliers becomes a data-driven task when considering factors such as load rating, seal effectiveness, lifespan, and cost. The following table outlines comparative benchmarks among leading bearing manufacturers:
Manufacturer | Model | Dynamic Load (N) | Sealing Type | Noise (dB) | Expected Lifespan (hrs) | Cost (USD) |
---|---|---|---|---|---|---|
SKF | 6202 2RS | 9800 | Double Rubber | 18 | 50,000 | 6.00 |
FAG | 6202-2RSR | 9600 | Double Lip | 19 | 47,500 | 5.80 |
NSK | 6202 DDU | 9500 | Contact Seal | 20 | 45,800 | 5.50 |
Peer Bearing | 6202 2RS | 9300 | Non-contact | 22 | 35,000 | 3.90 |
Premium brands such as SKF and FAG demonstrate higher dynamic load ratings and extended expected lifespans, with marginally increased costs. For industrial users prioritizing reliability and minimal maintenance, the investment in these top-performing models is often justified by lower lifetime operational costs.
Custom Solutions: Meeting Industry-Specific Demands
Industries as diverse as automotive, packaging, agriculture, and mining demand tensioner bearings that often exceed generic catalogue specifications. Customization may encompass advanced sealing technologies, special lubricants, integrated sensors for predictive maintenance, and tailored geometries compatible with bespoke mechanical layouts.
For example, agricultural combine harvesters operating in dust-rich fields challenge conventional seals; here, multi-lip labyrinth seals plant-reinforced with corrosion-inhibiting grease ensure both extended uptime and safety. Organizations with extreme washdown environments, such as food processing, frequently specify stainless steel 6202 bearings with food-grade lubricants and IP67 water resistance.
Application Case Studies: Performance in Action
Real deployment examples underscore the transformative impact of well-chosen tensioner bearing systems.
Case 1: In a European automotive assembly line, replacing legacy open-type bearings with double-sealed 6202 2rs bearings led to a recorded reduction in tensioner failures from 14% to under 2% annually, saving an estimated $120,000 in lost productivity.
Case 2: A mining conveyor operation upgraded to high dynamic load tensioner bearings and reported a mean time between failures (MTBF) extension from 14,000 to over 38,000 operating hours.
Case 3: In food-grade pharmaceutical processing, 6202 bearings with stainless housings and advanced seals enabled washdown protocols to run daily with zero lubricant ingress reported after a year’s cycle.
Best Practices for Bearing Selection, Installation, and Longevity
Optimal bearing performance is achieved through careful consideration during the selection and installation processes. Always analyze operating environment factors—temperature, humidity, contaminants, and vibration level—to narrow suitable bearing options. Install bearings using proper alignment tools and avoid excessive force, as misalignment is a leading cause of premature failure.
Periodic inspection and scheduled re-lubrication—especially under harsh conditions—prolong bearing integrity. Integrating vibration or temperature monitoring allows early detection of wear, reducing the probability of catastrophic equipment failure. For critical high-speed applications, consider bearing models equipped with factory-sealed lubrication for maintenance-free operation.
The Future of Tensioner Bearing Technology: Innovation and Sustainability
Ongoing advancements in tensioner bearing design are driven by evolving demands for energy efficiency, durability, and environmental performance. Adoption of engineered polymers, high-performance ceramics, and nano-coated seals are reducing friction coefficients and extending service intervals. With increasing emphasis on predictive maintenance and Industry 4.0 integration, smart bearing solutions now play a pivotal role in data-driven asset management.
Recent market research projects the global bearing market will exceed $186 billion by 2030, fueled by advancements in automotive and industrial automation sectors. Investment in high-performance 6202 2rs bearing variants and custom tensioner solutions ensures machinery reliability, superior efficiency, and lifecycle savings—cementing the tensioner bearing’s role as an essential component of modern engineered systems.
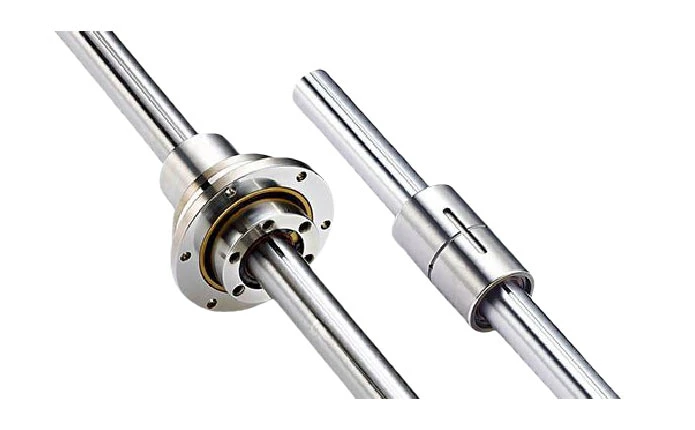
(tensioner bearing)